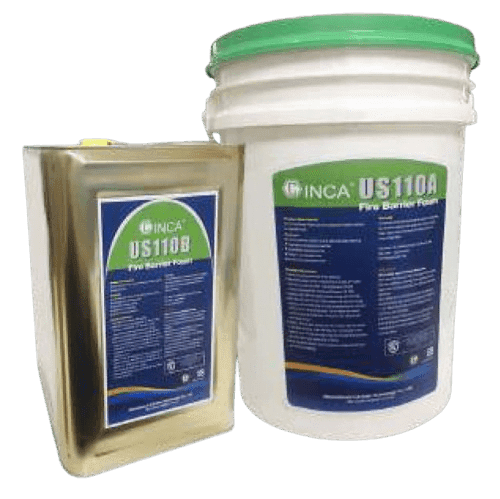
Fire Barrier Foam – US110
Industry leading Firestop Technology, US110 Fire Barrier Foam is a two component foam, consisting of separate A and B liquid components which, when mixed, form a flexible medium-density fire retardant foam. US110 Fire Barrier Foam is designed to seal large openings containing multiple penetrations such as cable bundles, cable trays and metallic pipes.
Prior to foaming, the liquid components remain fluid, allowing effortless sealing of any size and shape opening, making the product quicker and more efficient than traditional firestop methods. US110 Fire Barrier Foam’s fast expansion technology quickly fills voids, offering excellent protection from fire, heat transfer, smoke and gases. US110 Fire Barrier Foam offers unparalleled resistance to fire consumption, is halogen and asbestos free, durable and maintenance free.
Meets the intent of LEED® VOC environmental air quality requirements.
- Refer to applicable certification directory or www.paintoprotect.com for listed assemblies.
- Areas to be protected must be clean and free of oil, loose dirt, rust or scale. Installation temperatures must be between 50° F and 90° F (10°C and 32° C).
- Calculate amount of material required, based on the fact that a 23 kg kit yields 184,000 cm.
- US110 is supplied as two part components (Parts A & B). Settling and separation during storage is expected, therefore both components must be stirred with a clean paddle or suitable power mixer prior to use.
- Using a scale, weigh out and mix parts of US110A and US110B at a ratio of 7 – 4 . Mixing may be accomplished using a paddle mixer or other suitable power mixer in a container or by the use of automatic mixing and dispensing equipment. If paddle mixing is used, mix aggressively for 30 seconds.
- Immediately pour mixed foam into the penetration. Product rises and cures in 1- 5 minutes depending on temperature.
- Mechanical mixing and dispensing is recommended for large volume applications
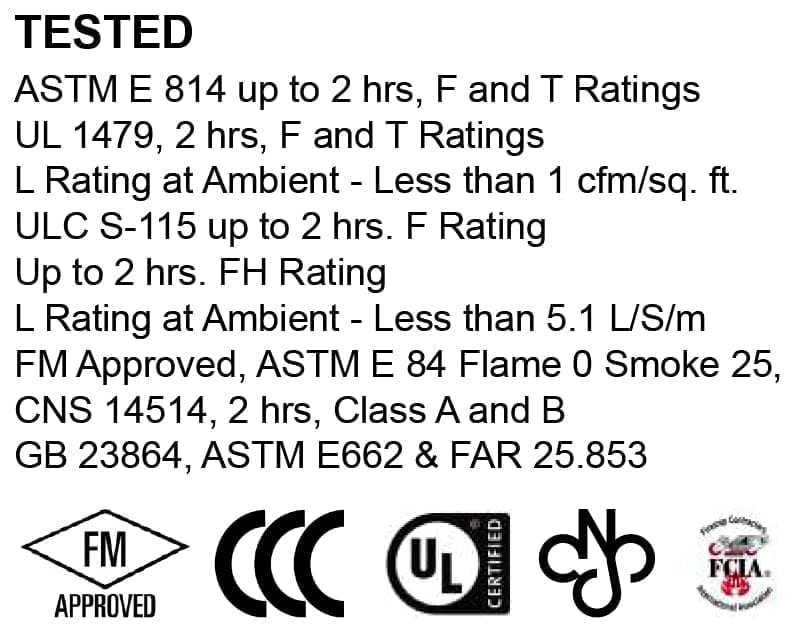
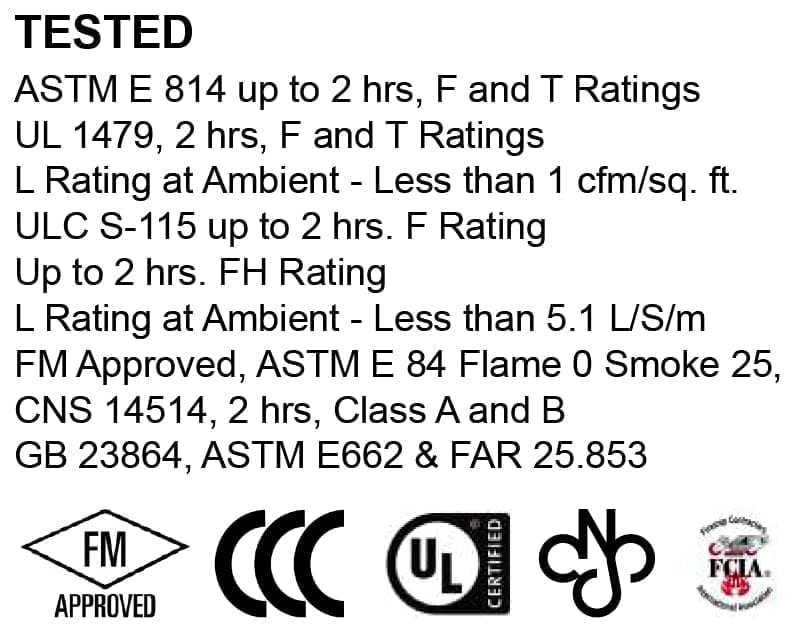
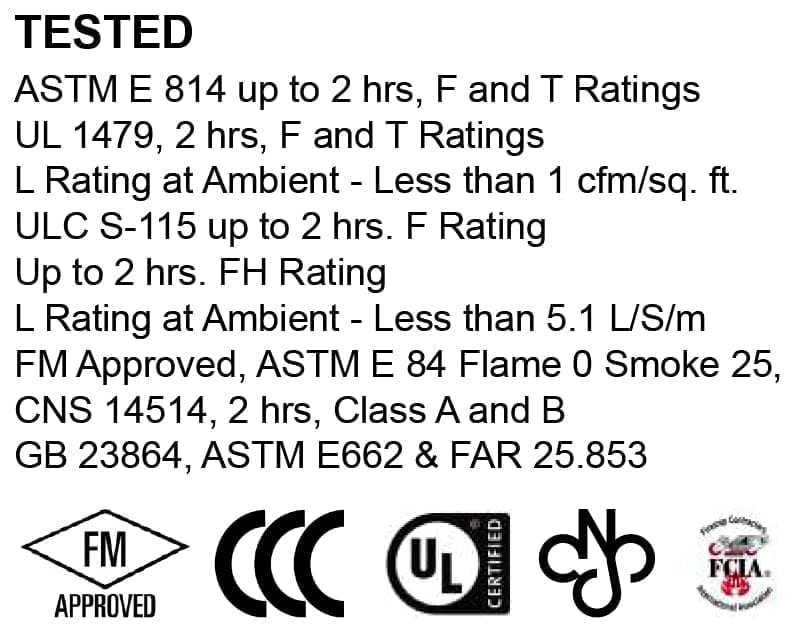
US110 A Color: Gray Packing: 14Kg/Pail
US110 B Color: Brown Packing: 9Kg/Pai
Foaming time: 1 – 5 min.
Optimum foaming temp: 50° F -90° F (10° C – 32° C)
Curing time: 24 hours
Volume expansion: 2.5 – 4 times
LO.I.: 732
Storage temp: 50° F – 77° F (15°C – 25°C)
In-Service temp: -13° F – 176° F (-25° C – 80° C)
Shelf life: 12 months
Intumescent expansion rate:2-5 times
Mix ratio A:B 7-4 by weight
Yield per kit: 184,000 cm3 (depending on ambient conditions)
Performance: 50+ years HOAC tested



Fire Barrier Foam – US110
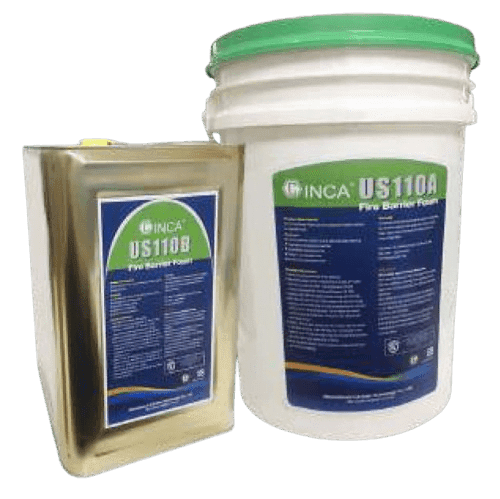
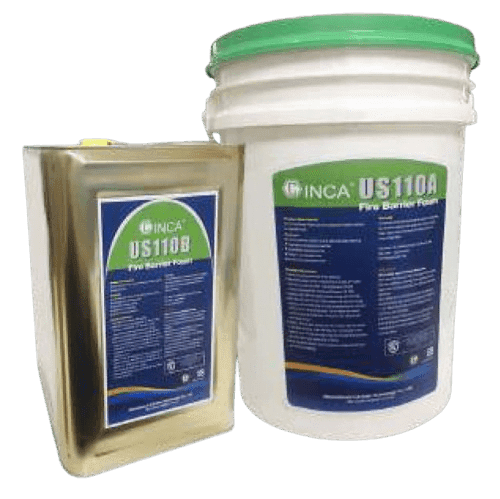
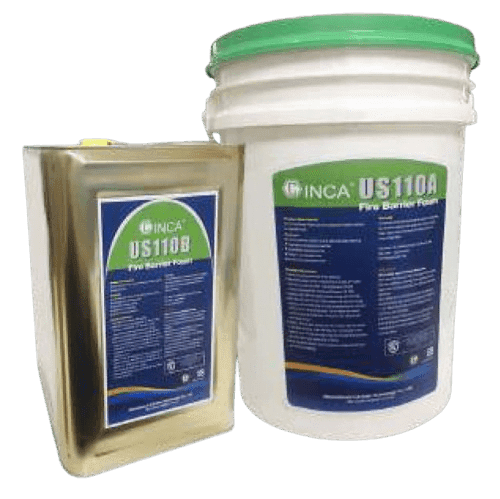
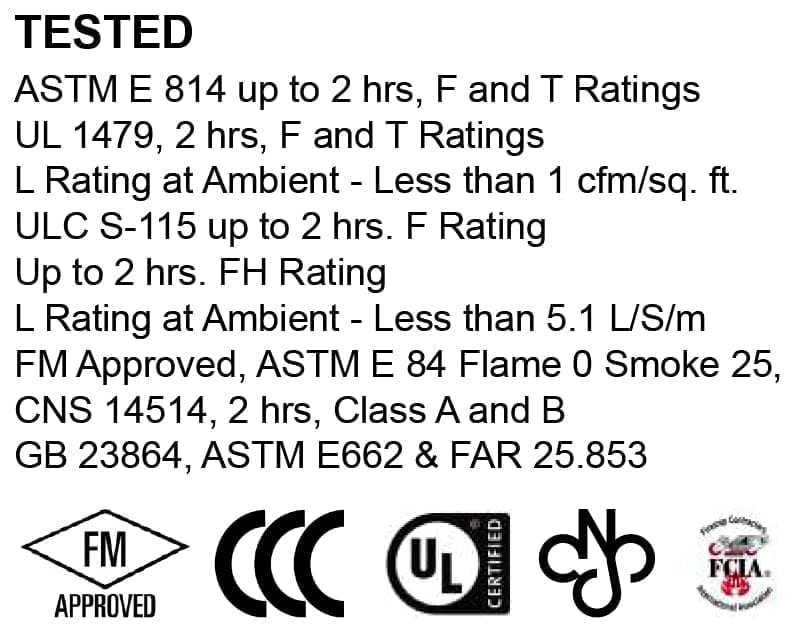
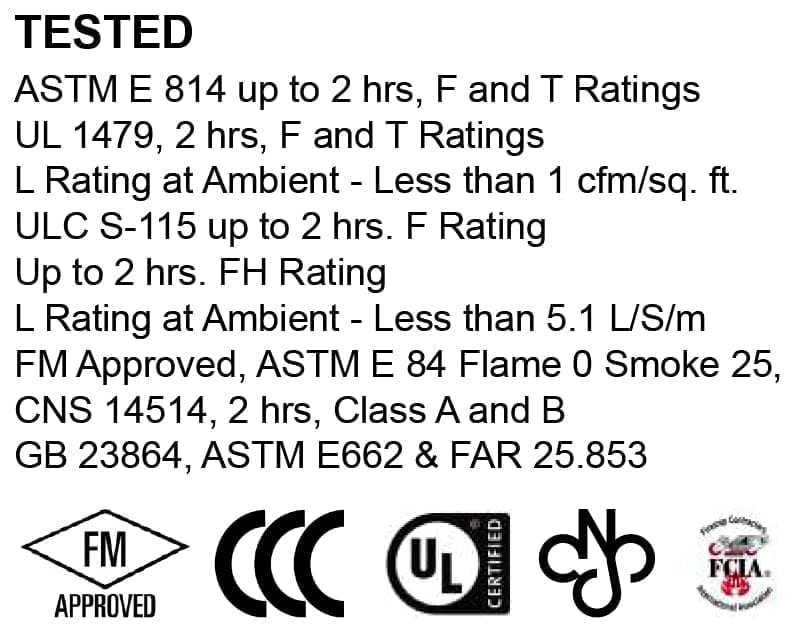
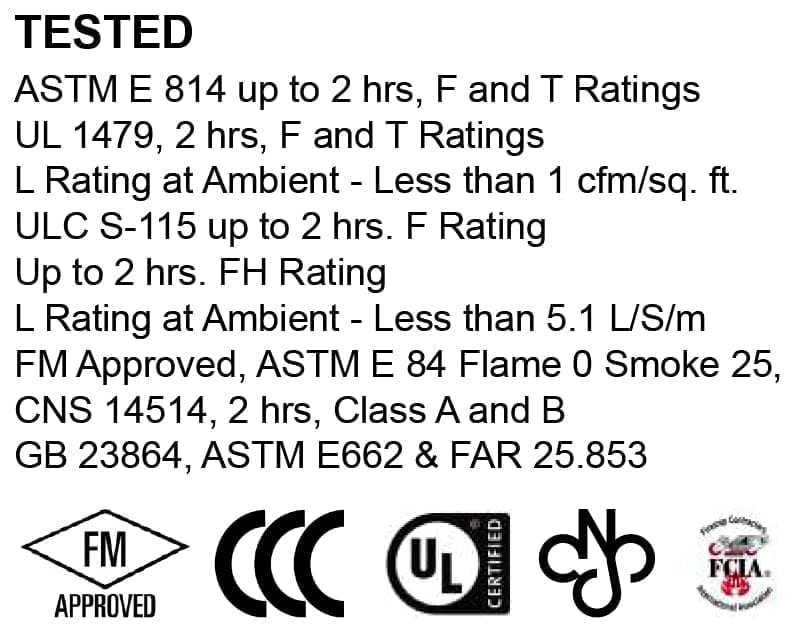
Industry leading Firestop Technology, US110 Fire Barrier Foam is a two component foam, consisting of separate A and B liquid components which, when mixed, form a flexible medium-density fire retardant foam. US110 Fire Barrier Foam is designed to seal large openings containing multiple penetrations such as cable bundles, cable trays and metallic pipes.
Prior to foaming, the liquid components remain fluid, allowing effortless sealing of any size and shape opening, making the product quicker and more efficient than traditional firestop methods. US110 Fire Barrier Foam’s fast expansion technology quickly fills voids, offering excellent protection from fire, heat transfer, smoke and gases. US110 Fire Barrier Foam offers unparalleled resistance to fire consumption, is halogen and asbestos free, durable and maintenance free.
Meets the intent of LEED® VOC environmental air quality requirements.
- Refer to applicable certification directory or www.paintoprotect.com for listed assemblies.
- Areas to be protected must be clean and free of oil, loose dirt, rust or scale. Installation temperatures must be between 50° F and 90° F (10°C and 32° C).
- Calculate amount of material required, based on the fact that a 23 kg kit yields 184,000 cm.
- US110 is supplied as two part components (Parts A & B). Settling and separation during storage is expected, therefore both components must be stirred with a clean paddle or suitable power mixer prior to use.
- Using a scale, weigh out and mix parts of US110A and US110B at a ratio of 7 – 4 . Mixing may be accomplished using a paddle mixer or other suitable power mixer in a container or by the use of automatic mixing and dispensing equipment. If paddle mixing is used, mix aggressively for 30 seconds.
- Immediately pour mixed foam into the penetration. Product rises and cures in 1- 5 minutes depending on temperature.
- Mechanical mixing and dispensing is recommended for large volume applications
US110 A Color: Gray Packing: 14Kg/Pail
US110 B Color: Brown Packing: 9Kg/Pai
Foaming time: 1 – 5 min.
Optimum foaming temp: 50° F -90° F (10° C – 32° C)
Curing time: 24 hours
Volume expansion: 2.5 – 4 times
LO.I.: 732
Storage temp: 50° F – 77° F (15°C – 25°C)
In-Service temp: -13° F – 176° F (-25° C – 80° C)
Shelf life: 12 months
Intumescent expansion rate:2-5 times
Mix ratio A:B 7-4 by weight
Yield per kit: 184,000 cm3 (depending on ambient conditions)
Performance: 50+ years HOAC tested


